Demand Flow Technology: The Future of Efficient Manufacturing Explained
In today’s competitive and ever changing markets, manufacturing industries must be agile, efficient, and customer-focused. Demand Flow Technology addresses these challenges by transforming production into a flexible and adaptive process that responds directly to customer needs. As a revolutionary approach to manufacturing, DFT reduces inefficiencies, enhances quality, and ensures timely delivery a critical combination for modern businesses.
What is Demand Flow Technology?
Demand Flow Technology (DFT) is a manufacturing methodology that aligns production with real-time customer demand, ensuring efficient operations while minimizing waste. Unlike traditional systems that rely on demand forecasting, DFT uses actual demand data to streamline processes, making production more agile and cost-effective. Developed as an evolution of lean manufacturing principles, DFT aims to create a smooth, demand-driven flow of goods and services.
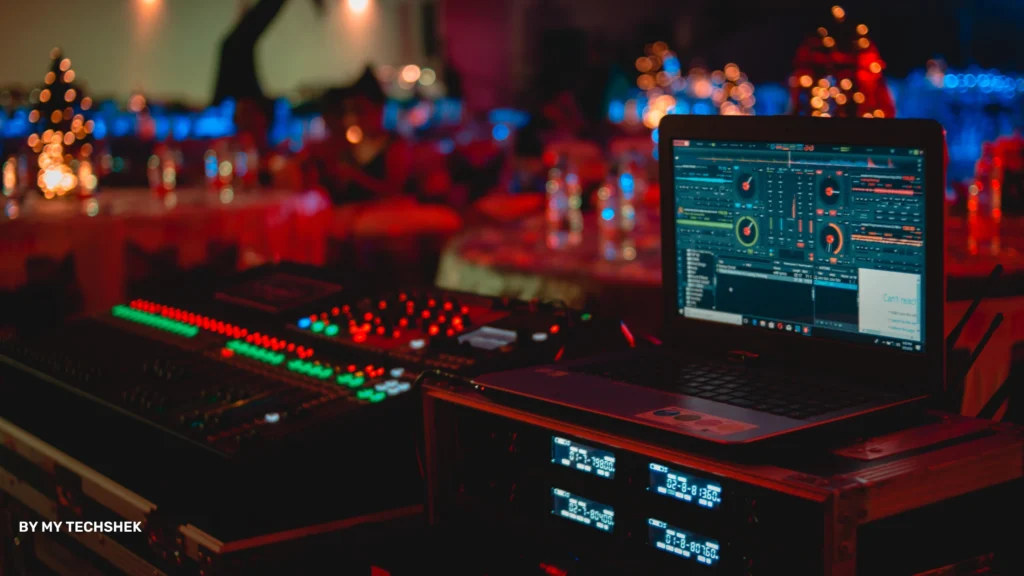
How Does Demand Flow Technology Work?
DFT operates by synchronizing production schedules with customer demand rather than relying on traditional forecasting methods. It achieves this through techniques like:
Flow Manufacturing:
This technique organizes production lines to ensure a continuous and uninterrupted flow of materials. By streamlining the workflow, businesses can reduce downtime and increase efficiency.
Pull Systems:
Instead of pushing products based on forecasted demand, components and materials are “pulled” into the production process based on actual customer orders. This minimizes overproduction and aligns inventory with real-time needs.
Takt Time Analysis:
This method calculates the optimal pace of production to meet customer demand rates, ensuring the right balance between production speed and order requirements.
Flexibility in Workstations:
Workstations are designed to adapt quickly to changes in product specifications or demand, ensuring businesses stay responsive to market shifts.
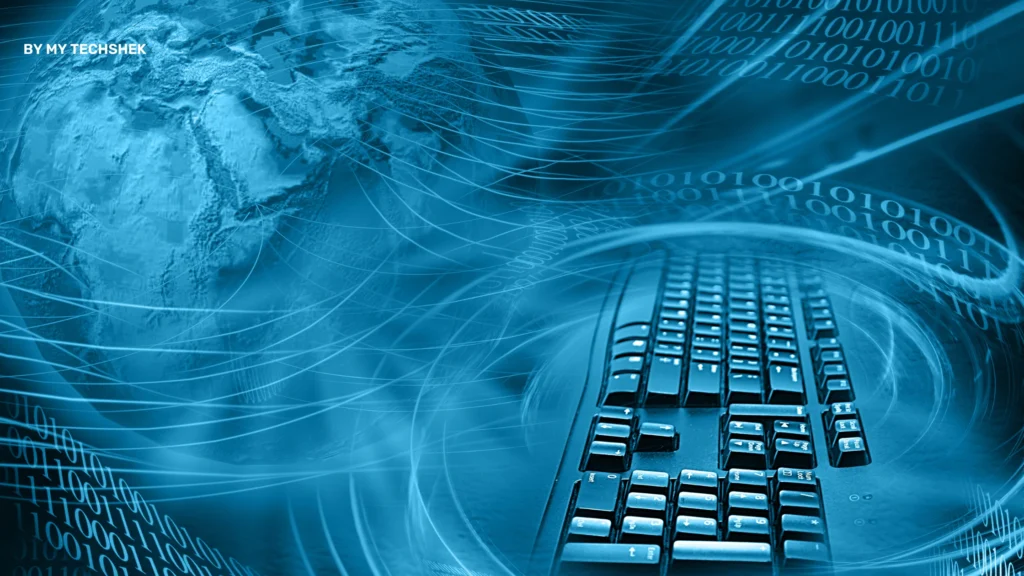
Importance of DFT in Modern Manufacturing
Demand Flow Technology is vital in today’s manufacturing for several reasons:
- Customer Responsiveness: Businesses can adapt swiftly to changing customer preferences, keeping them ahead in competitive markets.
- Cost Efficiency: Producing only what is needed reduces waste and inventory holding costs, improving profitability.
- Agility in Operations: DFT enables manufacturers to diversify their offerings and meet custom demands without compromising efficiency.
- Sustainability: By optimizing resource usage and reducing waste, DFT supports environmentally sustainable manufacturing practices.
What are the Core Principles of Demand Flow Technology?
The foundation of DFT lies in these core principles:
- Customer-Driven Production: Prioritizes actual customer demand rather than speculative forecasts, making the process more accurate and efficient.
- Flow Efficiency: Focuses on maintaining an uninterrupted movement of materials and tasks through the production process.
- Flexibility and Adaptability: Empowers businesses to pivot quickly in response to market dynamics.
- Waste Minimization: Encourages reducing excess inventory, idle time, and overproduction to improve overall efficiency.
- Continuous Improvement: Regularly evaluates and refines processes to ensure sustained growth and efficiency.
Components of Demand Flow Technology
Several key components make up DFT:
- Kanban Systems: These systems provide visual cues for inventory replenishment, ensuring a smooth flow of materials and preventing overstocking or shortages.
- Cellular Manufacturing: Groups similar tasks into specific production cells, optimizing the flow and reducing transit time between processes.
- Standardized Work Practices: Establishes consistent methods for tasks, improving efficiency and reducing errors.
- Real-Time Data Integration: Leverages modern technology to monitor demand fluctuations and adjust production accordingly.
- Employee Cross-Training: Provides workers with versatile skills to handle multiple tasks, ensuring adaptability and reducing dependency on specific personnel.
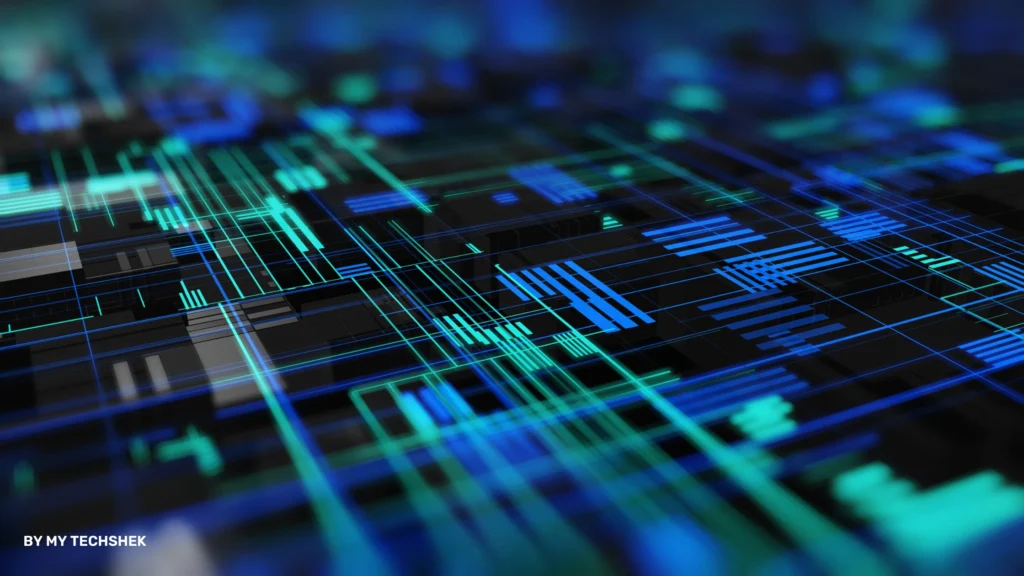
Implementation of Demand Flow Technology
Implementing DFT requires a structured and strategic approach:
- Assessment: Evaluate existing processes to identify inefficiencies, bottlenecks, and areas for improvement.
- Training: Educate employees about DFT principles and tools, fostering a culture of efficiency and adaptability.
- Process Reorganization: Redesign workflows to align with demand-driven strategies, eliminating unnecessary steps.
- Technology Integration: Adopt tools like demand monitoring software and Kanban boards to support real-time decision-making.
- Continuous Monitoring: Regularly review performance metrics and refine processes to ensure consistent improvement.
Benefits of Demand Flow Technology
Adopting DFT offers numerous benefits:
- Cost Savings: By producing only what is needed, companies save on storage, material costs, and waste management.
- Improved Quality: Streamlined processes ensure that products meet customer specifications with fewer defects.
- Enhanced Customer Satisfaction: Faster response to demand translates to timely deliveries and happier customers.
- Increased Productivity: Efficient workflows allow businesses to achieve higher output with the same resources.
- Sustainability: Reduced waste and optimized resource usage align with eco-friendly manufacturing goals.
Impact of DFT on Businesses Across Various Sectors
Demand Flow Technology has transformed several industries, including:
- Automotive: Flexible production systems enable manufacturers to meet diverse customer preferences efficiently.
- Electronics: Enhanced delivery times and reduced inventory costs improve profitability in a competitive market.
- Consumer Goods: DFT helps companies stay agile, responding quickly to seasonal and trend-driven demands.
- Healthcare: Precise, streamlined production processes ensure high-quality medical devices with reliable delivery schedules.
Case Studies: Demand Flow in Action
- Toyota: Revolutionized automotive manufacturing by adopting Kanban systems, improving production flow and reducing waste.
- Dell: Leveraged DFT principles to offer customizable computers with rapid delivery times, setting new industry standards.
- General Electric (GE): Applied DFT to appliance manufacturing, achieving significant efficiency gains and cost reductions.
Conclusion
Demand Flow Technology is a transformative approach to manufacturing, offering a demand-driven system that boosts efficiency, reduces costs, and ensures customer satisfaction. By integrating DFT principles, businesses can thrive in competitive markets, improve sustainability, and remain agile in the face of changing demands. As industries continue to evolve, DFT’s relevance and impact are poised to grow even further. For further guides about technology you can visit here.